Maximizing Efficiency with Rotary Screw Compressors:
Advanced Insights for Technical Experts
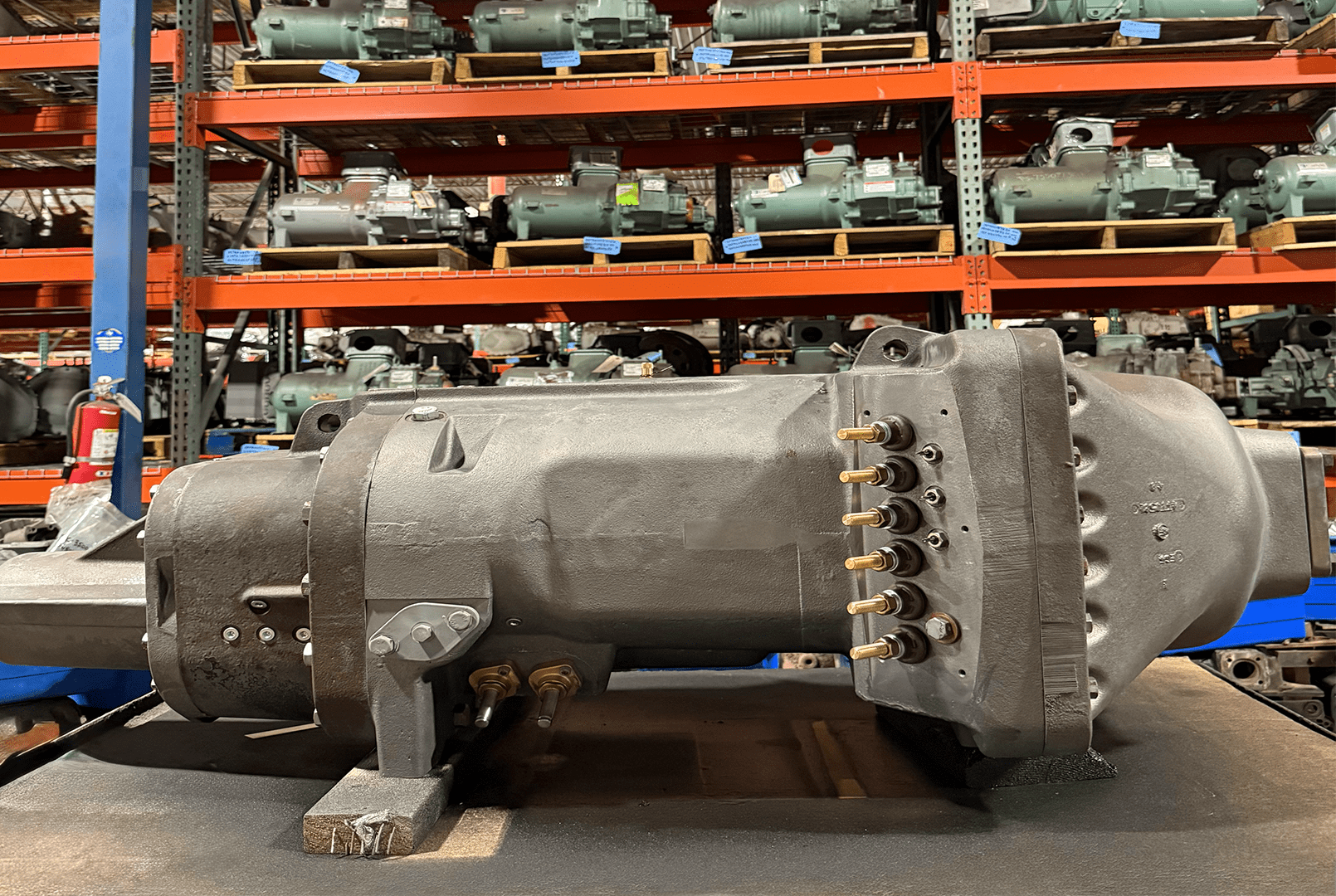
Rotary screw compressors are widely used in industries where compressed gas is essential for various operations, from manufacturing and automotive sectors to oil and gas. Although many professionals are familiar with the fundamental workings of rotary screw compressors, there are nuanced insights and advanced techniques that can help experienced technical experts optimize efficiency, extend equipment life, and reduce operational costs.
This blog delves into some lesser-known aspects of rotary screw compressors, offering a deeper understanding of their design, operation, and maintenance strategies, along with tips on how to achieve peak performance.
The Fundamentals of Rotary Screw Compressors
At the core of a rotary screw compressor are two helical rotors—one male and one female—that interlock within a chamber. As the rotors rotate, gas is trapped between them and compressed as the chamber size decreases. This continuous compression process results in a consistent stream of compressed gas.
Their simplicity, reliability, and ability to run without interruption are among the reasons why rotary screw compressors dominate commercial and industrial applications. However, many technical experts may not fully realize the impact that fine-tuning various operational parameters can have on efficiency and longevity.
Optimizing Rotor Profiles for Better Efficiency
Rotor design plays a critical role in the efficiency of rotary screw compressors. The male rotor, typically powered by a motor, interlocks with the female rotor, causing it to spin. The shape, pitch, and spacing of the rotors affect how much gas is trapped and compressed with each rotation.
Key Insight: One advanced approach to increasing efficiency is the use of asymmetric rotor profiles, which are more effective in reducing energy losses. In traditional symmetric profiles, the pressure on both rotors is the same, leading to more wear and tear. Asymmetric designs distribute the load more evenly across the rotors, reducing internal leakage and energy consumption. For technical experts, ensuring that the compressor system uses an updated rotor profile can significantly improve overall efficiency.
Variable Speed Drives (VSD) for Energy Savings
One of the most impactful technologies to pair with rotary screw compressors is the Variable Speed Drive (VSD).
VSDs adjust the compressor’s motor speed based on the real-time demand for cooling, ensuring that energy consumption matches output. By eliminating the need for the compressor to run at full capacity constantly, VSDs can reduce energy usage by up to 35%.
Key Insight: Although VSD technology is becoming more common, technical experts should be mindful of its application in specific environments. VSDs are most effective in scenarios where cooling demand varies, such as manufacturing plants with intermittent operations. However, for facilities with constant cooling demand, slide valve controlled compressors may be more cost-effective. It is crucial to assess air demand patterns before investing in VSD technology to maximize energy savings.
Heat Recovery: Tapping Into a Hidden Energy Source
One of the most overlooked opportunities in compressor efficiency is the potential for heat recovery. Rotary screw compressors generate a significant amount of heat during operation, with as much as 90% of the electrical energy used being converted into heat. This heat is often vented away as waste, but with the proper setup, it can be harnessed and repurposed.
Key Insight: Heat recovery systems can capture the heat generated by the compressor and use it for other processes such as space heating, preheating water, or supplying energy to other parts of the facility. For technical experts, designing a system that integrates heat recovery can provide a double benefit: reducing energy costs and improving the overall efficiency of the compressor system. Implementing this solution can save up to 50% of the energy typically lost as waste heat.
Air Quality Management: The Impact of Ambient Conditions
Many technical experts understand that ambient air quality affects compressor performance, but the full impact of air temperature, humidity, and particulate matter is often underestimated. Compressors operating in dirty or hot environments require more frequent maintenance and use more energy to maintain desired air pressure.
Key Insight: Installing high-efficiency air filters and ensuring proper ventilation around the compressor can drastically improve performance. For compressors in humid environments, a dryer or aftercooler may be necessary to prevent moisture from entering the system and causing corrosion or other damage. Keeping the intake air clean and cool allows the compressor to run more efficiently and reduces wear on internal components.
For technical experts seeking to optimize the performance of rotary screw compressors, a deeper understanding of advanced rotor profiles, VSD technology, lubrication practices, heat recovery, and air quality management can provide significant efficiency gains. By applying these insights and regularly assessing compressor performance, it’s possible to extend the life of the equipment, reduce energy consumption, and lower operational costs. As rotary screw compressors continue to play a vital role in industrial applications, leveraging these advanced techniques ensures that they perform at peak efficiency for years to come.