Understanding the Difference Between a
Rebuilt and Remanufactured HVAC Compressor Core
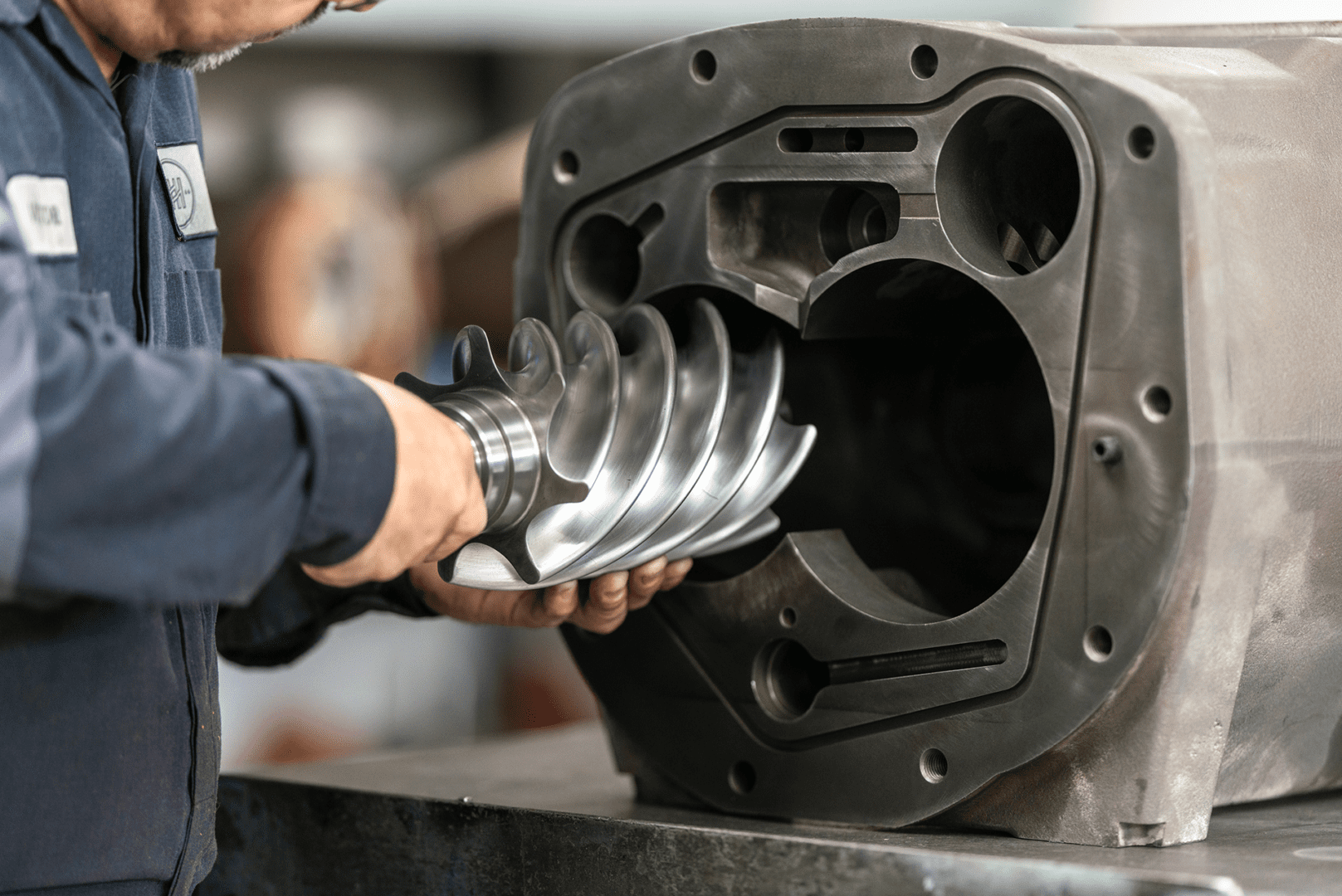
In the HVAC industry, compressor failures can be a significant issue, leading to costly downtime and repairs. While the terms “rebuilt” and “remanufactured” are sometimes used interchangeably, there are key differences in the processes and outcomes. Understanding these distinctions is crucial for making informed decisions about your HVAC systems.
This blog will explore the differences between rebuilt and remanufactured HVAC compressor cores, helping you decide which option is best suited for your needs.
What is a Rebuilt HVAC Compressor Core?
A rebuilt compressor core refers to a used compressor that has undergone repairs to restore functionality. The rebuilding process focuses on addressing specific failed components rather than completely overhauling the entire unit. Typically, during a rebuild, the technician identifies the broken parts, replaces them, and tests the compressor for basic operational function.
Here’s a more detailed look at the rebuilding process:
-
Inspection and Diagnosis: The technician inspects the compressor to identify which components have failed or are causing performance issues.
-
Replacement of Faulty Parts: Only the defective parts are replaced, such as valves, seals, or bearings, while the rest of the compressor remains largely untouched.
-
Testing for Functionality: After replacing the necessary parts, the compressor is tested to ensure it runs and can meet basic performance requirements. However, testing may not be as rigorous as in other processes like remanufacturing.
The rebuilt process is typically quicker and less expensive than remanufacturing, making it a more budget-friendly option in the short term. However, it may not always offer the same long-term reliability, as only the failed components are replaced, and the other parts, especially those with some wear, remain in use.
What is a Remanufactured HVAC Compressor Core?
A remanufactured compressor core, on the other hand, undergoes a far more extensive and meticulous process. Remanufacturing involves completely disassembling the compressor, inspecting all components, and replacing any parts that do not meet the original manufacturer’s standards. This process is more comprehensive than rebuilding and ensures that the remanufactured compressor performs as reliably as a new one.
Here’s a closer look at the remanufacturing process:
-
Complete Disassembly: The compressor is fully dismantled, and each component is removed, cleaned, and inspected.
-
Replacement of Worn or Outdated Parts: All critical components, such as bearings, seals, pistons, and valves, are replaced, regardless of whether they have failed or not. This ensures that the entire compressor is brought back to like-new condition.
-
Machining and Reconditioning: Certain parts, like rotors and casings, may be machined or reconditioned to restore them to their original specifications.
-
Rigorous Testing: Once the compressor is reassembled, it undergoes stringent testing under real-world conditions to ensure it meets or exceeds the original manufacturer’s specifications. Performance, efficiency, and reliability are all evaluated.
Remanufactured compressors are designed to function like new compressors and often come with extended warranties, giving businesses peace of mind that they are investing in a long-term solution.
Key Differences Between Rebuilt and Remanufactured Compressors
-
Scope of Repairs: The most significant difference between a rebuilt and remanufactured compressor is the extent of the repairs. Rebuilding focuses on fixing only the broken parts, while remanufacturing addresses all components, ensuring the compressor is essentially restored to its original condition.
-
Component Replacement: In a rebuilt compressor, only the defective parts are replaced, while many worn parts may remain. In contrast, a remanufactured compressor replaces all components that fail to meet the original standards, whether or not they’ve reached the point of failure.
-
Performance and Longevity: Remanufactured compressors are much more reliable and long-lasting than rebuilt units because they are restored to like-new condition and thoroughly tested. Rebuilt compressors may work in the short term but may not offer the same longevity or performance consistency due to potential wear on parts that weren’t replaced.
-
Testing Standards: Remanufactured compressors undergo extensive testing to ensure they meet OEM (Original Equipment Manufacturer) standards, while rebuilt compressors typically go through more basic functionality testing.
-
Warranty: Remanufactured compressors generally come with better warranties because they are closer to new in terms of performance. Rebuilt compressors may have limited or no warranties due to their more minimal restoration process.
Which Option is Right for You?
Choosing between a rebuilt and remanufactured HVAC compressor core depends on your priorities, budget, and operational needs.
-
Long-Term Reliability: For those seeking a long-term solution with performance comparable to a new compressor, a remanufactured compressor core is the best investment. The comprehensive nature of remanufacturing ensures greater reliability, efficiency, and durability.
-
Critical Applications: In situations where system downtime can be costly or dangerous, such as in hospitals, data centers, or high-demand industrial environments, remanufactured compressors are generally a safer option, offering better performance and warranties.
While both rebuilt and remanufactured HVAC compressor cores offer ways to restore compressor functionality, the differences in the processes and outcomes are substantial. At CSG Compressors, we understand the importance of choosing the right compressor for your application, and we offer ONLY high-quality remanufactured solutions that help businesses achieve their goals efficiently.